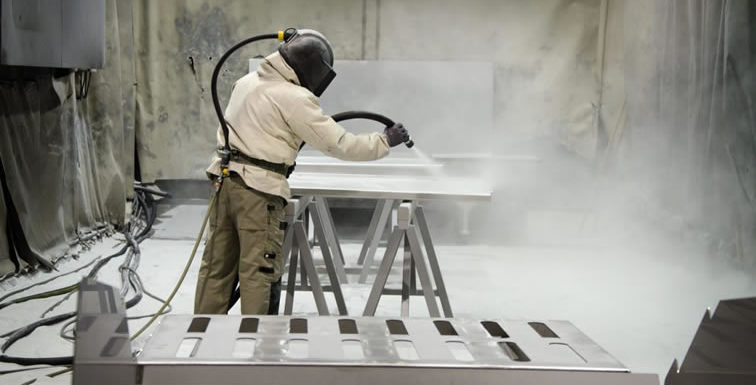
Abrasive blasting machine is more usually known as a sandblasting machine. The process of forcibly propelling a stream of abrasive material against a surface under high pressure to smooth a rough surface or roughen a smooth surface, shape a surface either remove surface contaminants. A pressurized fluid typically compressed air or a centrifugal wheel is utilized to propel the blasting material (usually called the media).
There are many variants of the process, using various media; some are highly abrasive, whereas others are more soothing. The most abrasive are shot blasting (with metal shot) and sandblasting (with sand). Slightly abrasive variants include glass bead blasting (including glass beads) plastic media blasting (PMB) beside ground-up plastic stock or walnut shells also corncobs. Some of these substances can cause anaphylactic shock to individuals allergic to the media A mild version is sodablasting (with baking soda). Also, some alternatives are barely abrasive or nonabrasive, such as ice blasting and dry-ice blasting.
Types of Abrasive Blasting Machine
Mobile dry abrasive blast systems are typically powered with a diesel air compressor. The air compressor produces a large volume of high-pressure air to a single either multiple “blast pots”. Blast pots are pressurized, tank-like containers, loaded with abrasive material, utilized to allow an adjustable amount of blasting grit into the main blasting line. The number of blast pots is dictated by the volume of air the compressor can produce. Fully furnished blast systems are often found mounted on semi-tractor trailers, offering high mobility also easy transport from site to site. Others are hopper-fed types making them lightweight also more mobile.
portable type Abrasive Blasting Machine
specification | compressor | Abrasive capacity |
Airoshot P7 150 | 1.5 cft | 42 ltr |
Airoshot P7 300 & 300R | 3 cft | 85 ltr |
Airoshot P7 500 & 500R | 5 cft | 142 ltr |
Airoshot P7 1000 & 1000R | 10 cft | 284 ltr |
Blast Cabinet
A blast cabinet is a closed-loop system that allows the operator to blast the part also recycle the abrasive. It normally consists of four elements; the cabinet (containment), the abrasive blasting system, the abrasive recycling system, also the dust collection. The operator blasts the parts from the outside of the cabinet by installing his arms in gloves attached to glove holes on the cabinet, viewing the part through a view window, turning the blast on and off using a foot pedal either treadle. Automated blast cabinets are also utilized to process large amounts of the same component also may incorporate multiple blast nozzles plus a part conveyance system.
There signify three systems typically used in a blast cabinet. Two, siphon also pressure, are dry and one is wet:
- A siphon blast system (suction blast system) does the compressed air to build a vacuum in a chamber (known as the blast gun). The negative pressure pulls abrasive into the blast gun where the compressed air leads the abrasive through a blast nozzle. The abrasive mixture travels through a nozzle that directs the particles toward the surface either workpiece.
Nozzles come in a variety of shapes, sizes, also materials. Tungsten carbide is the liner material most commonly used for mineral abrasives. Silicon carbide also boron carbide nozzles are more wear-resistant moreover are often used with harder abrasives such as aluminum oxide. Standard abrasive blasting systems and smaller cabinets use ceramic nozzles.
- In a pressure blast system, the abrasive is stored in the pressure vessel then sealed. The vessel is pressurized to the same pressure as the blast hose attached to the bottom of the pressure vessel. The abrasive is metered into the blast hose and conveyed by the compressed gas through the blast nozzle.
- Wet blast cabinets use a system that injects the abrasive/liquid slurry into a compressed gas stream. Wet blasting is typically used when the heat produced by friction in dry blasting would damage the part.
Blast Room
A blast room is a much larger version of a blast cabinet. Blast operators work inside the room to roughen, smooth, or clean surfaces of an item depending on the needs of the finished product. Blast rooms and blast facilities come in many sizes, some of which are big enough to accommodate very large or uniquely shaped objects like rail cars, commercial and military vehicles, construction equipment, and aircraft.
Each application may require the use of many different pieces of equipment, however, several key components can be found in a typical blast room:
- An enclosure or containment system, usually the room itself, designed to remain sealed to prevent blast media from escaping
- A blasting system; wheel blasting also air blasting systems are commonly used
- A blast pot – a pressurized container filled with abrasive blasting media.
- A dust collection system that filters the air in the room also prevents particulate matter from escaping.
- A material recycling or media recovery system to collect abrasive blasting media so it can be applied again; these can be automated mechanical or pneumatic systems installed on the floor of the blast room or the blast media can be collected manually by sweeping or shoveling the material back into the blast pot.
Additional equipment can be combined for convenience also improved usabilities, such as overhead cranes for maneuvering the workpiece, wall-mounted units with multiple axes that allow the operator to reach all sides of the workpiece, also sound-dampening materials applied to reduce noise levels.
Applications
The lettering also scratching on most modern cemetery monuments also markers are created by abrasive blasting.
Sandblasting can also be used to produce three-dimensional signage. This type of signage does consider to be a higher-end product as compared to flat signs. These signs often incorporate gold leaf overlay also sometimes crushed glass backgrounds which are called smalts. When sandblasting wood signage it allows the wood grains to show including the growth rings to be raised and is a popular way to give a sign a traditional carved look. Sandblasting can be done on clear acrylic glass also glazing as part of a storefront or interior design.
Sandblasting can be applied to refurbish buildings or create works of art (carved or frosted glass). Modern masks also resist facilitating this process, producing accurate results.
Sandblasting procedures are used for cleaning boat hulls, as well as brick, stone, and concrete work. Sandblasting is applied for cleaning industrial as well as commercial structures but is rarely utilized for non-metallic workpieces.
Abrasive blasting machine manufacturer
We airo shot blast the manufacturer, supplier, and exporter of portable sandblasting machines and Abrasive blasting machine’s components at a very low price in Jodhpur, Rajasthan, India.
We provide you the best quality of shot blasting machines and its components, we are the leading manufacturer, supplier of portable sandblasting machines,