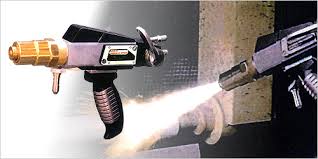
Zinc Spray Gun is applied to provide a protective coating on the surface of the subject. Zinc Metallizing is a versatile process that melts Zinc or Zinc Alloy metals, also then rapidly propels the molten Zinc particles onto a processed substrate, creating a lamellar or layered coating. Metallizing coating, or Thermal Spraying as it is often called, is a highly effective plus a proven method of corrosion prevention, giving galvanic as well as barrier coating protection to iron & steel. Zinc Metalizing applied to prevent the surface of the substrate from oxidation. This coating process is done after the surface treatment process with the sandblasting machine. Zinc metalizing gun provides a thick coating layer over the surface of the substrate.
How does Zinc Spray Coating work?
Most protective coating systems for steel function acting as a wall between the steel and the corrosive environment. If these passive and permeable barriers are damaged or penetrated, moisture and oxygen can reach the steel causing rust including eventual coating failure. A zinc metalized coating also offers barrier protection; however, the electrochemical relationship between zinc and steel allows a zinc coating to give cathodic protection as well.
A zinc metalized coating will protect the steel galvanically. it will degenerate in preference to steel, continuing to protect as long as any zinc remains in the immediate area. The surface of a metalized coating permits excellent adhesion of sealers and topcoats. The effect of this combination is a synergistic coating system that will protect the underlying steel and require little or no maintenance for many years.
Advantages of Zinc Spray Coating
Long Term Protection:
A sealed, Zinc Spray Gun coating can realistically provide 30 years of corrosion protection in rural environments and 5 to 25 years in urban and coastal areas. Exacting atmospheric conditions will not rust steel protected by a zinc metalized coating.
Versatility:
Coating thickness can be varied. This is important because the protection achieved is directly proportional to the weight of a zinc metalized coating. Severe atmospheric conditions and longer life of the subject requires an increased coating thickness. The thickness can also vary in different areas of the same structure, such as troublesome flange edges, giving needed extra protection. Applied zinc metalized coatings will not mud crack, run or sag when applied over .006m thickness.
No Drying/Curing Time:
A zinc metalized coating bonds instantly allowing for immediate application of wash primers and sealers. Because there is no drying time, additional labor costs, lengthy setup times and constant maintenance scaffolding costs are reduced or eliminated.
No Size Limitation:
Whether the job is in your shop or in the field, there is no limit to the size of the structure to be coated with Zinc.
No Warpage:
The surface being coated remains at ambient temperatures. Therefore, a zinc metalized coating does not distort the shape of the steel. nor will it affect its metallurgical structure. Weld embrittlement, over tempering and steel strength losses are not a concern when metalizing with zinc.
No VOCs:
The coating industry is interested in protecting the infrastructure without damaging the environment around it. A zinc metalized coating is inorganic also does not contain volatile organic compounds that can harm the environment.